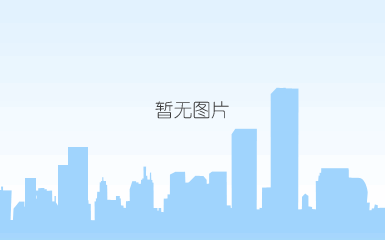
装备制造集团中央机厂认真贯彻落实省委“32字要求”,强化管理、苦练内功、深挖潜力,提升产品质量,引进先进设备,培养新型技术人才,加快智能化建设步伐,推动企业高质量发展。
深挖内潜增效益。该厂紧紧围绕“降减提”目标,制定了《中央机厂“降本增效、减人提效、提效增效”实施办法》,成立了领导组,下设3个专项工作组,分别负责降本增效、减人提效、提效增效方面的考核,并对开拓市场、账款清收、优化工艺、技术革新、修旧利废等环节作了具体规定。实行全闭环管理,通过全员参与、分口督导、严格考核、持续改善,采取有效成本费用管控措施,实现降本增效。同时,考核组成员不定时深入全厂各生产单位,就车间每月上报的项目和数据进行实地考查,并按规定每月召开1次考核会,对“降减提”工作进行严格考评,每季度进行1次专项评价,按评价结果给予奖罚,推动“降减提”工作落地落实。
严格考核提质量。该厂领导深入生产末端细节,找“病灶”,开“处方”,把责任落实到人、把压力传导到底,不断“焊牢”层层衔接、环环相扣的“责任链条”。严格实施科学的质量管理和质量关键点控制,号召全厂员工进行“大家来找茬”,深入开展产品质量“大检查、大整改、大提升”活动。下料车间作为液压支架生产的源头首道工序,形成自检和互检、日检和抽查相结合的模式,从编程到数控切割再到坡口,保证每一道工序都经过多次检验,避免不合格产品流入下一道工序;技术中心建立了党、政、工、团、妇“五位一体”质量管理生产体系,对液压支架零部件进行认真梳理和审核,从材料选型、公差要求、坡口整形、组点焊接等各个环节入手,对在生产中容易出现的问题做到绝不遗漏、绝不放过;质检中心组织抽查组不定期、不定点的对每个车间进行产品质量抽查,对查出的问题坚持“三不放过”原则,做到原因不查清不放过,责任部门和个人未受处理、未受教育不放过,没有防范措施不放过,形成工艺流程有人管、施工现场有人盯、每道工序有人验、产品成型有人检的良好氛围。
科技创新促发展。该厂在成本控制和技术创新上下足功夫,通过优化生产布局、淘汰落后工艺、引进先进设备等举措,为企业发展增添实力。技术中心积极组织研究高端液压支架,通过针对钢板特性、焊缝、结构性设计等方面进行优化改造,进一步提高了液压支架的产品质量,并实现了通用件标准化互换模式,为日后的产品保养及维修提供了诸多便利,得到了用户的一致好评。同时,开展各类技能培训和技术比武,不断提升员工技术水平,特别是对于新引进设备,采取现场实践与培训相结合的办法,大力培养新型技术人才,为企业发展提供人才支撑。